2020 is changing how food manufacturers see crises. Is your plant prepared?
What is Crisis Management?
The past few months have – or should have - changed the way we look at our day-to-day operations and maybe you’ve learned a bit about how prepared or unprepared you were for a crisis as the pandemic has unfolded. New updates, new recommendations, new scientific findings, and so forth kept us all working in a dynamic mode to offer the best solutions. The industry has learned a lot while pivoting and thinking on its feet. It should also change the way each of us looks at Crisis Management forever.
What is a Crisis?
The definition of crisis is very straight forward, noted as “A time of intense difficulty, trouble or danger.” The synonyms associated with the word are just as bleak. Does anything positive come to mind when you hear these words? Catastrophe, calamity, cataclysm, emergency, disaster, predicament, plight, mess, dilemma, quandary, setback, upheaval, dire straits, hard times, hardship, adversity, distress, difficulty.
Managing Crises
Traditionally, crisis events include scenarios like a product recall, natural disaster, or an event that has been created from within your organization or externally. Today, we’re also seeing a greater number of crises impacting the food supply chain and food safety – and all at once – from border and transportation issues to raw ingredient shortages, production bottlenecks and a lack of qualified workforce.
First, assess your own capabilities to address such a seemingly simple word. Are you someone who can ALWAYS think on your feet and react calmly to what might be required of you in a crisis? Look around you and identify others in your organization who can ALWAYS think on their feet and also react calmly and join your crisis response team. Even with the appropriate team in place, most manufacturers then need a plan to guide you through how to react responsibly and effectively as a team to get through the crisis and regain control to resume business as usual. Having a framework for navigating through these situations gives us confidence and focus to handle the event.
Next, each of the possible crisis scenarios should be considered and assessed for your location to determine if contingency plans need to be developed for managing such events. Some of these events lead to product recalls, some lead to business disruption, some impact employee welfare. Your crisis team may come up with more scenarios to consider for your location, but these categories offer a starting point.
If current events haven’t yet impacted your operation, you’ve likely read about the repercussive impacts they’re having on others across the food supply chain and around the world. When they do, the impacts can be devastating. That’s why it’s critical to be prepared. Today, more so than ever.
Product Recalls
Every food manufacturer should already have a product recall plan in place. Your first response may be to ask “If My Product Has Never Been Recalled, Why Do I Need a Recall Plan?,” which we answered in a recent blog. If you don’t have a plan or your recall team isn’t in place, our Traceability & Recall Online course may be beneficial.
Natural Disasters
There is zero human control when natural disasters are involved, so you will need pre-planning in place to deal with the aftermath of the events. Some weather events like a hurricane/typhoon, blizzard and tornado may allow for preparation. Other events like an earthquake, forest fire, flood or an avalanche/landslide may strike without warning. If your location might be a target for any of these events, consider contingency planning preparation to respond to the impact to your operations and employees. Further, which of these natural disasters could potentially impact your product and customers?
Internally-Created Crises
These are the crises we strive daily to prevent, but sometimes even the best and most routinely-practiced protocols are not followed. Negative issues that manifest internally in the operating environment can be devastating and always require a quick response and calm leadership to minimize the impact.
Risk likelihood may increase for some of these issues depending on internal factors out of your control. Labor negotiations may put a facility at higher risk for intentional adulteration or workplace violence issues. Workforce turnover may make equipment and process failures more likely due to lack of experience or lack of expertise in operational procedures. One plant in the United States had an immigration raid that resulted in 89 percent of the sanitation department and 54 percent of production employees being taken from the facility. The majority of tenured operators and skilled labor at the plant were gone within a single hour mid-afternoon. This is a crisis.
You need to intimately know your operation and honestly assess your vulnerabilities, considering the probability of internally-created crisis events occurring.
Externally-Created Crises
We have absolutely NO control over these events, but planning your response for mitigating the impact can provide some element of preparedness. We’ve all now had first-hand knowledge of how a pandemic can affect the health of our workforce, our supply chain, and our ability to get product out the door. Have you incorporated those learnings into your crisis plan so you’re better prepared for the next one?
Supply Chain Crises
Supply chain disruption should be considered in the initial event risk assessment. These are also events you cannot control and that are considered external, but that that strike suppliers of goods and services to your operation. We must have plans in place to deal with the operational impact of these events. In today’s global economy, suppliers may be in the same town or located on the other side of the world. Some ingredients carry more risk than others. You may be susceptible to each of these events and others, which makes them worth analyzing to determine whether a plan is needed to mitigate their impacts.
Prepare for a Crisis
A robust Crisis Management Plan will give you confidence and the tools we need to face whatever the future may hold. Having a plan also means you have worked with our crisis team to evaluate the probability and risk of the various crises and how they will impact our operation.
Related Training
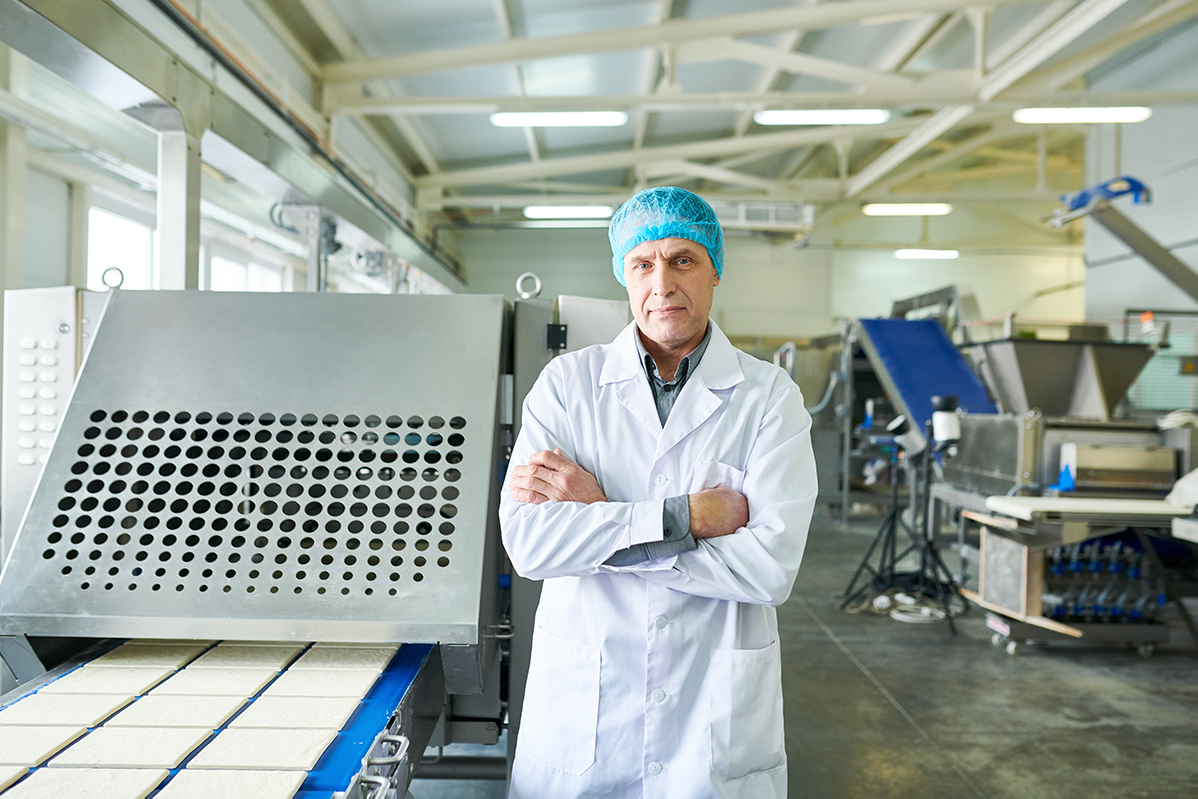
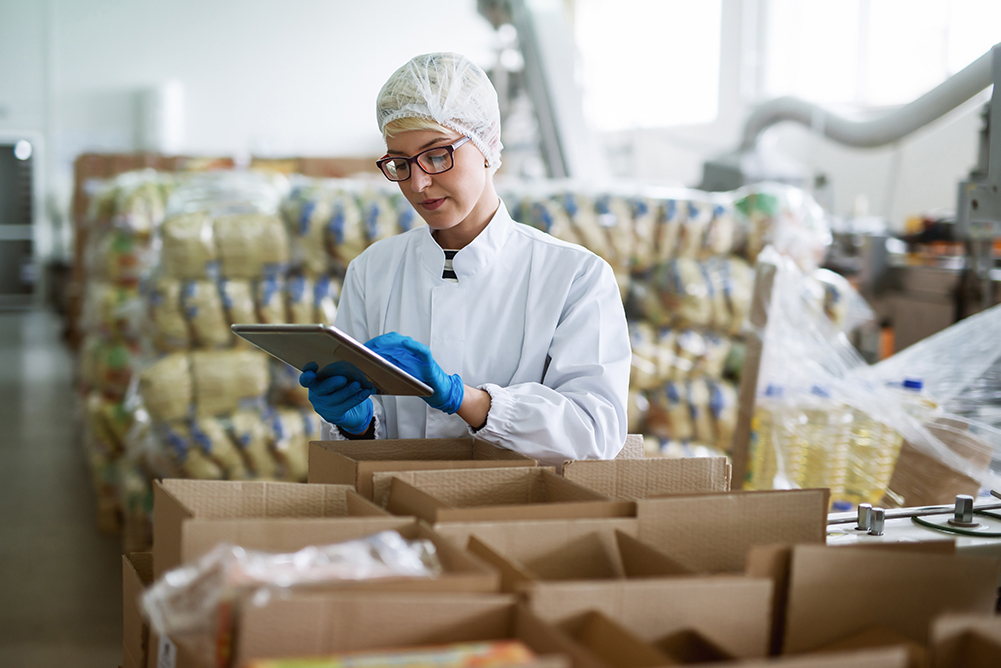