Tip of the Week: Backflow Prevention
Backflow is the unwanted reverse flow of any liquid, solid, or gas into the potable piping system. There are two forms of backflow: backsiphonage and backpressure.
Backsiphonage occurs when contaminants are pulled into the potable water supply. This may happen if there is a broken water main or when nearby fire hydrants are in use. The drop in water pressure can pull materials into the water line. The effect is similar to the sipping of a soda by inhaling through a straw, which induces a flow in the opposite direction.
Backpressure happens when contaminants are pushed into the potable water supply. This can happen if there is a loss of pressure in the potable water supply, similar to the scenarios described for backsiphonage, or when there is increased pressure on the non-potable supply, such as with a pump or from heat from a boiler. Back pressure-backflow is created whenever the downstream pressure exceeds the supply pressure which is possible in installations such as heating systems, elevated tanks, and pressure-producing systems. An example would be a hot water space-heating boiler operating under 15-20 lbs. pressure coincidental with a reduction of the city water supply below such pressure (or higher in most commercial boilers). As water tends to flow in the direction of least resistance, a backpressure condition would be created and the contaminated boiler water would flow into the potable water supply.
Backflow preventers are used to interrupt backsiphonage and backpressure. There are five typical types of backflow preventers. These are:
1. Atmospheric Vacuum Breaker (Air Gap): This is a vertical, physical separation between the end of a water supply outlet and the flood level rim of the receiving vessel, such as at a sink.
2. Anti-Siphon Valve: This is a one-directional valve with a spring-loaded flap.
3. Pressure Vacuum Breaker: This is a mechanical backflow preventer with one check valve and one air inlet valve. It is equipped with a shut-off valve and test cocks. This is effective against backsiphonage, but not backpressure.
4. Reduced Pressure Backflow Preventer: This is a mechanical backflow preventer with two independent check valves and a pressure differential relief valve. It is also equipped with a shut-off valve and test cocks.
5. Double Check Backflow Preventer: (Not to be confused with a dual check backflow preventer, which does not include a shut-off valve or test cocks.) This is a mechanical backflow preventer with two check valves in a row. However, there is no vent to allow air to enter the lines or allow water to exit. It uses the tight seals of the valves to prevent backflow.
When selecting and installing a backflow preventer it is imperative that local codes are complied with. Not all types of backflow preventers are approved for all types of applications.
Once plant locations where backflow can occur have been identified, it is necessary to ensure that a backflow preventer is installed. These locations include, but are not limited to, where water enters a vessel, such as a kettle, and where hoses are connected to faucets to fill mop buckets. A list or map of all of the backflow preventer locations must be developed and kept current. It is recommended that the serial numbers of the backflow preventers also be recorded with the corresponding location for tracking purposes. This will help to link documentation of checks with specific devices and locations.
Once installed, annual checks of each backflow preventer are required. These checks must be performed by someone who is properly trained and often requires a licensed plumber. Results of all checks must be maintained and any faulty preventers must either be repaired or replaced. Most cities conduct annual checks of the backflow preventer at the main valve to ensure that there will be no backflow into the city water supply. This test does not demonstrate that backflow issues internally at the facility are controlled. Each device must be tested.
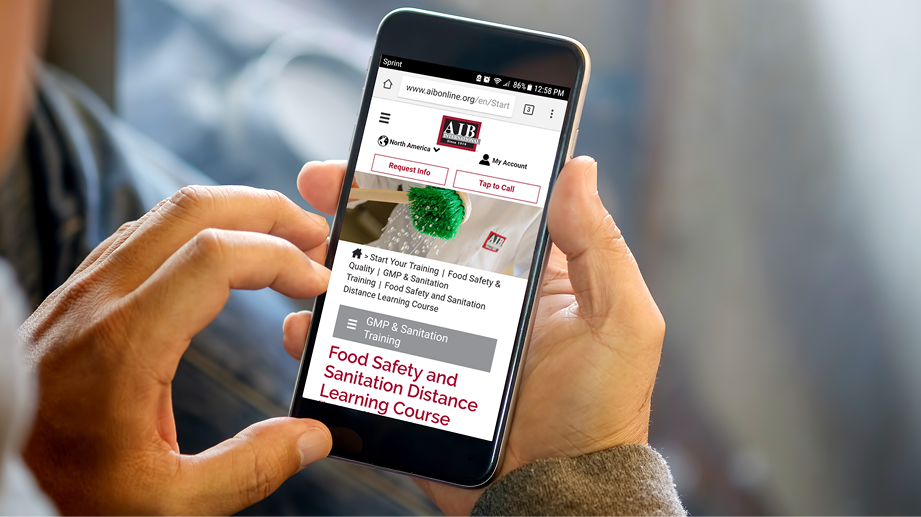